Increasing Resource Efficiency and Sustainability at Goodwill Industries of Kanawha Valley, Inc.
Goodwill Industries of Kanawha Valley, Inc. is a charitable organization in the state of West Virginia, USA. It is one of 161 independent, local Goodwill agencies across the USA and Canada. The non-profit organization provides career training and supportive services to help people with employment barriers.
This is all funded through donated clothing that the organization collects from their 15 thrift stores and 100 clothing banks.
Reusing clothing is a cornerstone of the world’s sustainability journey. At Goodwill, their services are not only about providing much-needed community services; it’s also about encouraging textile recycling. And it’s easy to see why. According to the Resources, Conservation and Recycling Journal, for every 2lbs (1kg) of cotton provided by secondhand clothing, you save approx. 65kWh.
That’s the equivalent of running your refrigerator for 18 days.
Problem: Overflowing donations bin and lost donations
Goodwill was facing overflowing clothing banks and lost donations. At the same time, their operational set-up could benefit from optimization. Donations bins were being serviced too early, resulting in unnecessary expenses (diesel and staff hours). And with Goodwill’s rural areas and a limited number of trucks, this was particularly costly, with some bins located an hour’s drive away.
Goodwill wanted a more efficient approach to their operations. After narrowing it down to four technologies, Goodwill decided to partner with Nordsense due to the solution’s proven ability to function optimally in rural locations, as well as its user-friendly online platform.
Objectives
- Reduce overflowing bins
- Prevent lost and contaminated donations
- Optimize collection services
- Increase resource efficiency
“In the past, our donation bins were prone to overflow. We emptied them regularly, but since we didn’t have a clear or digitized overview of how much they were being used, our collection services would often arrive too late. This caused a serious inventory issue, and unfortunately, we ended up losing valuable donations and
resources.
The Nordsense smart solution has completely changed this. The data from our smart sensors means we can continually monitor fill levels and pick up containers before they overflow.”
Kassia Lilly, Vice President of Operations at Goodwill Industries of Kanawha Valley, Inc.-.
Improving Resource Efficiency and Increasing Donations
At Goodwill, donated clothing and textiles are valuable resources. The clothing is inventory for thrift stores and acts as an essential stream of revenue to fund charitable projects. But the collection services arrived at the wrong time – sometimes too late.
This meant that donors were greeted by full or overflowing clothing banks. People would end up dumping their donations on the street beside the container, rendering them contaminated and unusable. This would also attract illegal dumping, as people would dump larger items, such as broken furniture, resulting in extra cleaning costs for Goodwill.
![Donation Bin Photo[72] Goodwill uses sensors to optimize its collections](https://nordsense.com/wp-content/uploads/2023/04/Donation-Bin-Photo72-243x300.png)
Overflowing bins render donations unusable and attract illegal dumping
Smart waste technology is helping them service their clothing banks at exactly the right time – before they start overflowing and losing valuable donations. The Nordsense platform provides a clear overview of container fill levels in real-time. So, operations and logistics managers can remotely monitor the usage of their clothing banks and quickly schedule services for full donation bins.
The flexibility of the Nordsense solution meant that it could be adapted to specific needs. For Goodwill, unwanted textiles are not waste – they are a resource. They want to collect donations as soon as possible to get them on the shop floor and keep stores adequately stocked.
Therefore, Goodwill’s sensors define a container as full when it is at 50% capacity to ensure that clothing is collected as quickly as possible.
Overflowing clothing banks and late collection services don’t only mean lost donations. It also means lost resources and revenue.
More Textile Recycling and Better Sustainability
Goodwill is one of the original recyclers. They try to find a purpose for all donations. Even if donations are damaged and can’t be sold on the shop floor, the organization does its best to ensure items do not end up in a landfill. Its goal is to reduce the number of textiles going to landfill – where it typically takes 30-40 years for clothing to biodegrade.
Convenience is a key aspect of this sustainability mission. Studies show that if a donor has to travel more than five miles (8km) to recycle unwanted clothing, they are more likely to toss it in the garbage.
For Goodwill, more donation bins in more convenient locations are needed to increase textile recycling. Pairing the bins with smart sensors and implementing a data-driven approach to logistics means that Goodwill can expand their program while still obtaining a good ROI. The data ensures that they don’t need to increase their already limited staffing, fuel consumption, and truck resources.
Optimizing Collection Routes
Donation patterns are highly unpredictable. Sometimes clothing banks are almost empty for weeks. Sometimes they become full and overflowing in a matter of hours. This unpredictability has been a challenge for Goodwill and the supply chain. Without data, it’s impossible to know how often clothing banks are used.
The clothing banks are spread out across different counties in West Virginia. Some of them are in rural locations and at least an hour’s drive away from each other. Before using smart sensors, drivers were sometimes taking unnecessary routes to service clothing banks that were empty.
Thanks to smart sensors, Goodwill can optimize their routes and avoid unnecessary collections. Instead of operating on static and fixed schedules, where drivers are regularly sent out on the same routes, they can prioritize its collections. The organization now uses event-driven schedules, so drivers are only sent out to pick up clothing banks when needed.
Thanks to smart sensors, Goodwill can optimize their routes and avoid unnecessary collections. Instead of operating on static and fixed schedules, where drivers are regularly sent out on the same routes, they can prioritize its collections. The organization now uses event-driven schedules, so drivers are only sent out to pick up clothing banks when needed.
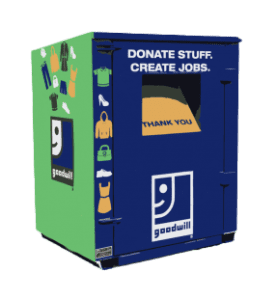
Challenges: Donation Theft and Vandalism
Goodwill’s containers are a prime target for crime. Sometimes, people climb inside and steal donated clothing. Together with Nordsense, Goodwill uses the data and drivers’ feedback to address these issues.
By setting the bin’s capacity to 50% in the platform, they are better positioned to collect the materials faster and keep the area around the donation bins tidier before incidents of theft and vandalism.
Curious how the Nordsense solution can help optimize your operations?